Nascono dalla stampante 3D le eliche di Italian Propellers
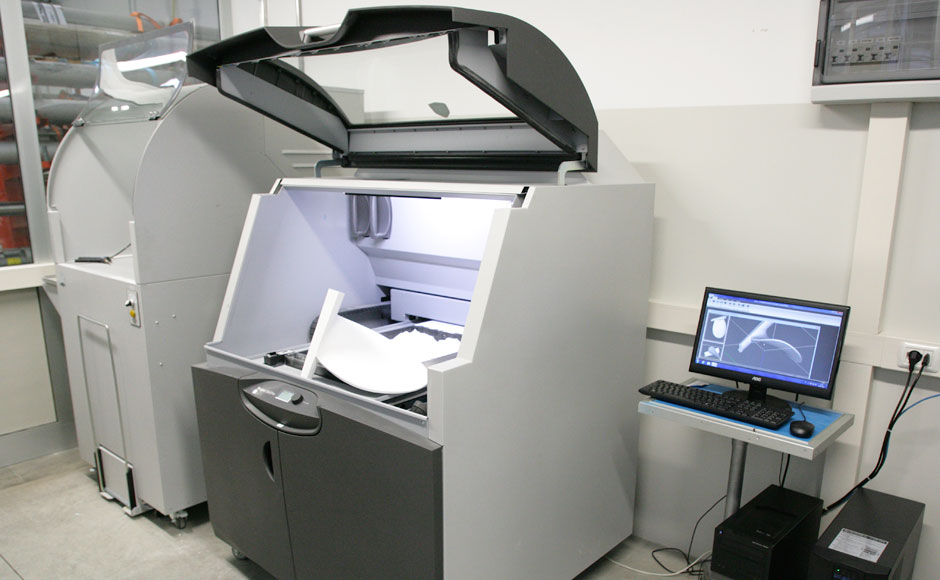
La realizzazione del modello alla stampante 3D è certamente la fase più spettacolare, ma dietro a un’elica Italian Propellers c’è molto di più.
L’attenzione è subito per la stanza a temperatura controllata che si trova in officina nel nuovo stabilimento. È lì che si trovano le due stampanti tridimensionali che da alcuni anni sono diventate l’insostituibile terminale di tutti i progetti che nascono in Italian Propellers. Ma il processo di nascita di una nuova elica (come di qualsiasi altro elemento di una trasmissione) è ben più complesso, anche se la fase affidata alle due stampanti è certamente importante per finalizzare tutto quanto è stato elaborato in precedenza. Ripercorriamo attraverso il racconto di Marco Belotti, che insieme al fratello Claudio è il cuore e la mente di Italian Propellers, e le foto di Sergio Airoldi, la storia della nascita di un’elica.
Le tre fasi di Italian Propellers
Che si tratti di un’elica, o di un altro elemento della trasmissione, la sequenza della nascita e costruzione di un nuovo progetto segue sempre la stessa trafila ed è difficile, per non dire impossibile, individuare un momento più importante dell’altro. Progettazione, realizzazione dello stampo e costruzione sono indissolubilmente legati uno all’altro.
Quindi tutto inizia sul tavolo di Marco Belotti e sui suoi computer: “La base di partenza è sempre la barca su cui l’elemento che andiamo a studiare, poniamo un’elica, deve essere montata. Quindi: lunghezza, larghezza, dislocamento, motorizzazione con potenza e giri, rapporto di riduzione dell’invertitore e tipo di trasmissione sono i dati fondamentali da cui partire. Da quella che viene individuata come la soluzione ottimale si verifica quali modelli abbiamo già disponibili e, nel caso nessuno risponda a quanto individuato, si procede a realizzare un nuovo progetto che viene sviluppato sia in 2D sia in 3D. Non c’è solo da individuare diametro, passo e numero di pale, ma anche gli spessori delle varie sezioni che devono coincidere con i parametri previsti dal RINA o dagli altri enti preposti nel caso si debba poi navigare in acque internazionali, come spesso succede”.
“Una volta definita la forma finale dell’elica che vogliamo costruire - prosegue Marco Belotti -, è il momento di studiare quello che sarà il suo modello di fonderia, quindi prevedere il sovrametallo che dovrà poi essere asportato in fase di lavorazione meccanica per arrivare al prodotto finito. Anche questo passaggio è sviluppato in 3D e poi salvato con un apposito software per la stampante. In realtà le stampanti sono due che scegliamo in base alla dimensione dell’elica: per quelle più piccole, fino a 550/600 mm di diametro, usiamo il modello a filo di abs; per quelle più grandi (che spesso stampiamo divise anche in tre sezioni) la tecnologia a gesso in polvere che viene solidificato da un solvente. Quello che si ricava è già il modello pronto per essere avviato in fonderia”.
Il resto della storia, la terza fase, riprende l’iter conosciuto: la fusione rientra in Italia Propellers dalla fonderia e viene lavorata sulle macchine a controllo numerico e quindi verificata con le strumentazioni che ne permettono le successive certificazioni di finitura, nel rispetto della normativa ISO 484/2 e secondo la richiesta del cliente. Solo a qual punto l’elica è pronta per essere spedita al cantiere.