La fibra di carbonio in barca: vera esigenza o solo marketing? Il parere dell'esperto
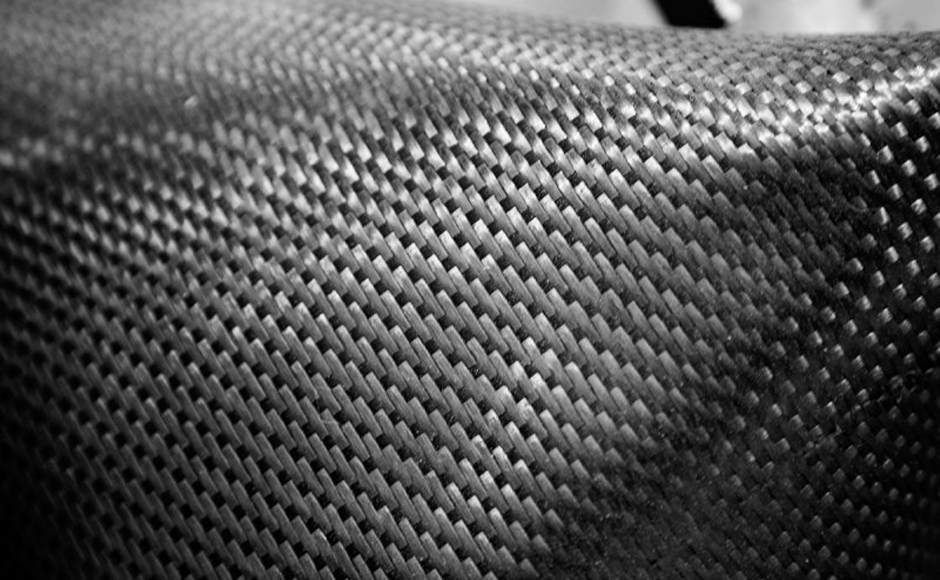
Com’è fatta la fibra di carbonio? Quali pregi e quali difetti ha? A cosa serve in barca e fino a che punto conviene utilizzarla? Lo abbiamo chiesto a Sergio Abrami, progettista nautico dal 1971 e docente e coordinatore del master di Yacht Design dell’ISAD (Istituto Superiore di Architettura e Design).
La fibra di carbonio viene ormai usata abbondantemente nella produzione di qualsiasi oggetto in cui si ricerchi una grande resistenza meccanica ma senza sacrificare la leggerezza, proprio ciò che serve anche nel prodotto barca. E in ambito nautico si sente spesso enfatizzare l’utilizzo del carbonio, laddove ne è stato fatto uso, come una fra le più importanti peculiarità di quella barca, ma il rapporto costi/benefici è davvero vantaggioso oppure è più uno strumento degli uomini di marketing per enfatizzare un valore aggiunto, sicuramente reale, ma non del tutto necessario?
Cerchiamo allora di capirne di più, entrando nella fibra di carbonio accompagnati da Sergio Abrami, che dice:
Per progettare bene, come “racconto” ai miei studenti del master di Yacht Design dell’ISAD, bisogna conoscere “al meglio” materiali e tecnologie. Questa conoscenza permetterà di evitare errori e il cattivo o improprio uso di materiali non idonei, oltre a sprechi e di conseguenza costi.
Uno dei materiali attualmente più “cool” è la fibra di carbonio. È un materiale relativamente giovane. I primi utilizzi in campo militare risalgono agli inizi degli anni ’60 dello scorso secolo.
Allora era considerato un “materiale strategico”. Ricordo da ragazzino di aver letto spy story incentrate sul nero e rigido materiale, ma ora è argomento e materiale d’uso di stilisti, creativi e pubblicitari in tutti i settori. Restando nel mondo della nautica: reali vantaggi o pure operazioni di marketing? Questo è l’interrogativo che tra le righe mi è stato dato come input per trattare questo argomento.
Quando il carbonio risulta indispensabile o logico da utilizzare
Premetto che non sono un fanatico della fibra nera, anzi mi dà personalmente un po’ di fastidio quando è utilizzata a sproposito. In certi casi ritengo però la fibra di carbonio davvero indispensabile, come nel caso delle piattabande (sono le facce parallele al fasciame delle nervature, per esempio costole, serrette, longitudinali del fondo ecc.) in UD-C con anime in rinforzi di carbonio biassiali +/- 45°, ovvero più genericamente per quasi tutte le strutture di rinforzo trasversali e longitudinali.
Mi dà fastidio quando vedo “contrabbandare” il carbonio come fosse un amuleto, un toccasana, una parola magica che tiene lontane le disgrazie. “Sì, non si preoccupi, è tutto in carbonio”… mi son sentito dire tante volte quando, da verificatore sportivo, ispezionavo componenti realizzati da costruttori spesso molto dotati di grande manualità, di tecnica, ma completamente digiuni di conoscenze nel campo strutturale.
Oggi, oltretutto, il carbonio costa molto meno rispetto a prima, tant'è che nel corso dei decenni si è passati dall’uso discreto e parsimonioso delle fibre UD di carbonio, motivato da banali questioni economiche, all’attuale uso massiccio di laminati, pelli di strutture a sandwich e fasciami solidi in solo carbonio. Per chi non lo sapesse, nei primi anni ’70 dello scorso secolo, il carbonio costava 600.000 lire al kg (si pensi che in quel periodo un’utilitaria come la A112, equivalente all’attuale Lancia Y, costava circa 900.000 lire), oggi invece il carbonio, grezzo, costa intorno ai 20 euro al kg, che salgono a 60-75 euro nel caso di tessuti tecnici tipo il twill.
Carbonio parola magica dunque? No, il carbonio, o fibra di carbonio, non è una parola magica, ma se il suo utilizzo in una struttura è ben progettato e ben applicato, è una fibra che in molti casi può salvare vite umane, come ha fatto soprattutto in campo motoristico sportivo, anche in motonautica.
Nelle gare offshore
il tasso di incidenti
resta ancora alto,
ma sono crollati
i casi di morte
dei piloti, grazie
anche alla fibra
di carbonio con cui
sono fatte le safety cell
Nello specifico parlo delle “safety cell”, il complesso canopy + cockpit che protegge il pilota in caso di incidente. La motonautica, specie quella d’altura (offshore) è sempre stata uno sport pericoloso. La lista dei piloti deceduti dal 1940 ad oggi è impressionante (guarda qui). Basti pensare che le pressioni d’impatto sono legate al quadrato della velocità e che la velocità degli offshore è aumentata rapidamente col passare degli anni.
Oggi gli incidenti non sono calati, anzi, ma la serie delle fatalità si è fortunatamente fermata al 2013 (Classe 1 in Gabon). E il merito è anche del carbonio utilizzato nelle safety cell, oltre naturalmente per la maggior parte ai continui miglioramenti e verifiche predisposte dall’autorità sportiva internazionale, la UIM (Union International Motonautisme).
Tutto carbonio ha dunque senso?
Certamente sì nel campo dei mezzi da competizione (motonautica, regate di alto livello, multiscafi da regata e foiler). In questi casi il gioco vale la candela, per non parlare poi delle safety cell inserite anche in costruzioni più convenzionali, dove le sue caratteristiche, esaltate nelle strutture a sandwich , sono fondamentali per garantire la resistenza richiesta con il minimo peso e dove le quantità in opera sono relativamente modeste.
Per quanto riguarda il diporto, un uso intelligente di comune fibra di vetro nei fasciami a sandwich combinato con strutture di carbonio può essere la soluzione vincente. Massimo risultato con il minimo dispendio di energie (economiche) e in termini di combustibili.
Rischi connessi alle caratteristiche del materiale
Uno dei rischi procurati dal carbonio è relativo alla conducibilità elettrica, e non parlo solo di folgorazione (vedi le canne da pesca in carbonio che sfiorano i cavi dell’alta tensione), ma a un cattivo isolamento di componenti e di attrezzature di coperta su un’imbarcazione full carbon.
Questa caratteristica però è di grande aiuto per riconoscere a colpo sicuro il “vero carbonio” dal “finto carbonio”: un semplice controllo con un banale ed economico tester permette di fugare gli eventuali dubbi. Il vetro come ben sappiamo è un ottimo isolante, il carbonio per contro è un buon conduttore.
Il rischio maggiore in realtà è la sua fragilità, che porta alla rottura senza segni premonitori.
Durante la guerra in Vietnam – metà anni ’60 – vennero proposte delle barelle elicotterabili per evacuazione feriti dal fronte, strutturate con sottili e leggerissimi tubi in carbonio in sostituzione di quelli in lega leggera di alluminio. Raccontano che il povero marine, che doveva simulare un ferito barellato, rischiò il dissanguamento perché il troppo sottile prototipo di carbonio si ruppe come un tubo del neon in vetro.
Questo spiega perché per lungo tempo negli anni ’70 si utilizzarono ibridi di carbonio e kevlar, specie nelle costruzioni nautiche.
I vantaggi, comunque sono di più. L'uso sapiente del carbonio, soprattutto dell’UD sulle piattabande delle strutture, permette di ridurre le dimensioni di queste ultime conservandone la rigidità. Si riducono i pesi e si aumentano i volumi utili interni delle imbarcazioni (anche quelle da diporto in PRFV “convenzionale”). Non avreste mai sospettato dei benefici di una fibra strutturale per incrementare il comfort abitativo a bordo, vero?
Senza dubbio, poi, l’alleggerimento delle strutture dei mezzi di locomozione (imbarcazioni incluse) porta anche a benefici ambientali: meno massa, meno potenza e meno consumi per ottenere pari prestazioni. La fibra nera dunque è “verde”! E vi sembra poco?
La fibra di carbonio vi sorprenderà sempre e la troveremo sempre più spesso a bordo.
Ma diffidate
della fibra
di carbonio
a vista
Dimenticavo … non lasciatevi ingannare dal carbonio a vista, sono l’equivalente nautico dei richiami per le allodole… Bello, elegante da vedere, ma solo in fotografia, come i cruscotti carbon look delle auto “zarre” o dei ciclomotori dei ragazzini portati ad aprire le marmitte per dare l’impressione della velocità.
Il carbonio a vista è una vera bestialità, sì perché non c’è gelcoat trasparente che tenga: gli UV danneggiano la matrice della prima lamina esterna molto più velocemente di quanto non si creda. Così si ottiene un oggetto più pesante (a parità di resistenza meccanica), perché si porta a spasso una lamina meno performante, quella esterna alterata dagli UV (raggi Ultra Violetti), che si traduce in un peso inutile… vedi foto al microscopio elettronico.
Il carbonio visto con l'occhio tecnico
La fibra di carbonio è prodotto dall'ossidazione, la carbonizzazione e grafitizzazione dei precursori organici ricchi di carbonio che sono già in forma di fibra.
Il precursore più comune è poliacrilonitrile (PAN), perché è in grado di fornire le migliori proprietà delle fibre di carbonio, ma la fibra può anche essere ottenuta da pece in mesofase o da cellulosa (i.e. rayon).
La variazione del processo di grafitizzazione produce sia le fibre ad alta resistenza (lavorate a circa 2.600°C) o fibre ad alto modulo (lavorazione a circa 3000°C) con altri tipi di mezzi. Una volta formata, la fibra di carbonio subisce un trattamento superficiale applicato per migliorare l’adesione alla matrice (in genere di base epossidica ed una apprettatura che serve per proteggerlo durante la movimentazione).
Esistono diverse tipologie di fibra caratterizzate essenzialmente da un diverso modulo elastico E a flessione.
Il modulo di elasticità è una grandezza, caratteristica di un materiale, che esprime il rapporto tra tensione e deformazione nel caso di condizioni di carico monoassiale e in caso di comportamento di tipo "elastico" del materiale. È definito come il rapporto tra lo sforzo applicato e la deformazione che ne deriva. La sua unità di misura è il MPa ovvero megaPascal espresso in (N/m²). (i.e. 10 MPa = 1.02 Kgf/mm2).
Le caratteristiche meccaniche delle diverse tipologie di fibra di carbonio
Commercialmente a seconda delle loro caratteristiche meccaniche, le fibre di carbonio possono essere suddivise in :
• GP (General Performance): caratterizzati da una minore resistenza meccanica; hanno un modulo di Young non superiore a 200 GPa
• LM (Low Modulus): presentano valori bassi del modulo di Young
• HP (High Performance): caratterizzati da una maggiore resistenza meccanica
• HT (High Tensile Strenght): presentano valori elevati della resistenza a trazione (maggiore di 3000 MPa) e valori standard del modulo di Young (intorno a 150-300 GPa)
• IM (Intermediate Modulus): presentano valori moderati del modulo di Young (intorno a 275-350 GPa)
• HM (High Modulus): presentano valori elevati del modulo di Young (maggiori di 300 GPa)
• UHM (UltraHigh Modulus): presentano valori elevatissimi del modulo di Young (maggiori di 600 GPa).
Valori che per i non addetti ai lavori, come gli appassionati di nautica che ci seguono, forse possono dire molto poco. Ma è il confronto che convince.
Attenzione che esiste anche il black glass disonestamente spacciato per carbonio. In realtà il cosiddetto black glass ha caratteristiche meccaniche completamente diverse dal carbonio: è comune vetro E pigmentato.
Ecco il confronto tra le caratteristiche dei diversi materiali usati nel settore nautico.
• Vetro E – il più diffuso nelle costruzioni nautiche e non
· Densità: 2,55 g/cm3
· Modulo elastico: 72 GPa
· Resistenza meccanica a trazione: 2400 MPa
• Vetro S – il migliore , per applicazioni speciali
· Densità: 2,48 g/cm3
· Modulo elastico: 90 GPa
· Resistenza meccanica a trazione: 4500 MPa
Fibra di carbonio HM
· Densità: 1,75 g/cm3
· Modulo elastico: 531 GPa
· Resistenza meccanica a trazione: 5650 MPa
Come certamente avrete notato la resistenza a trazione è “appena” poco più del doppio del vetro E, ma è il modulo elastico che conferisce le caratteristiche di rigidezza del manufatto che è davvero impressionante: ben oltre sette volte quello del vetro E!
Sergio Abrami